Error message
- Deprecated function: dirname(): Passing null to parameter #1 ($path) of type string is deprecated in drupal_get_path() (line 2970 of /mnt/volume_sgp1_08/cgtglasstrading/public_html/includes/common.inc).
- Deprecated function: dirname(): Passing null to parameter #1 ($path) of type string is deprecated in drupal_get_path() (line 2970 of /mnt/volume_sgp1_08/cgtglasstrading/public_html/includes/common.inc).
- Deprecated function: dirname(): Passing null to parameter #1 ($path) of type string is deprecated in drupal_get_path() (line 2970 of /mnt/volume_sgp1_08/cgtglasstrading/public_html/includes/common.inc).
- Deprecated function: dirname(): Passing null to parameter #1 ($path) of type string is deprecated in drupal_get_path() (line 2970 of /mnt/volume_sgp1_08/cgtglasstrading/public_html/includes/common.inc).
- User warning: The following theme is missing from the file system: flat_metro. For information about how to fix this, see the documentation page. in _drupal_trigger_error_with_delayed_logging() (line 1184 of /mnt/volume_sgp1_08/cgtglasstrading/public_html/includes/bootstrap.inc).
- Deprecated function: dirname(): Passing null to parameter #1 ($path) of type string is deprecated in drupal_get_path() (line 2970 of /mnt/volume_sgp1_08/cgtglasstrading/public_html/includes/common.inc).
- Deprecated function: dirname(): Passing null to parameter #1 ($path) of type string is deprecated in drupal_get_path() (line 2970 of /mnt/volume_sgp1_08/cgtglasstrading/public_html/includes/common.inc).
- Deprecated function: dirname(): Passing null to parameter #1 ($path) of type string is deprecated in drupal_get_path() (line 2970 of /mnt/volume_sgp1_08/cgtglasstrading/public_html/includes/common.inc).
You are here
Reflective Glass
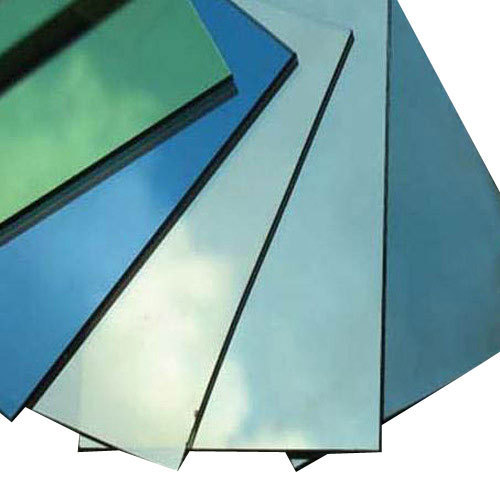
Reflective glass is essentially ordinary float glasswith a metallic coating that cuts off solar heat. This special metallic coating also provides a one-way mirror effect, preventing visibility from the outside and thus preserving privacy. Reflective glass is used primarily for structural façade glazing.
There are two different ways of manufacturing reflective glass - production pyrolitic process and vacuum (magnetron) process.
1. Production Pyrolitic (On-line):
In this process, semi-conducted metal oxides are directly applied to the glass during float glass production, while the glass is still hot, in the annealing lehr. These coatings are called hard coatings, and are relatively less harmful to the environment.
Pyrolytic Glass
In summary, pyrolytic glass is a reflective glass that has had a coating applied to it during float glass manufacture. The coating is fused to the glass at 1200o C. The best feature of this product is its durability; it can be easily handled like a standard square of glass. It can also be easily cut, heat strengthened or toughened. Pyrolytic glass is sometimes referred to as “hard coat” reflective. Since it is processed online, it works out to be cost-effective.
2. Vacuum (Magnetron) Process (Off-line):
In this process, one or more coats of metal oxide are applied under a vacuum to finished glass. The coatings applied by this technique are soft and require protection from the external environment; they are therefore applied on the inner side of glass panes. Their low resistance makes them better off when used in a double glazing system. Cost-wise, this glass is relatively expensive.